Wireless sensor combines capabilities
There’s no lack of useful information in most process industry applications, but accessing and collecting it is often difficult or impossible due to all the networking and programming hurdles required to get data where it needs to go. To bridge these traditional chasms and enable users’ asset performance management (APM), Yokogawa Corp. of America is transforming its wireless, modular Sushi Sensor and support system as part of its new Industrial Internet of Things (IIoT) Vibration Plant Asset Management (PAM) program. PAM will allow equipment, processes and plants to use continuous monitoring and predictive analytics to detect issues sooner, and enable their operations and maintenance personnel to collaborate, so they can be more efficient with their resources.
Just as sushi combines rice, fresh fish and other ingredients, PAM is expanding Sushi Sensor’s data-gathering capabilities about facility conditions, and combining them with many other formerly separate functions. It starts with Sushi Sensor XS770A wireless, three-axis vibration and surface temperature sensor that measures velocity at 0 to 20 mm/s, acceleration at 0 to 130 m/s², and temperature at -20 °C to 85 °C. The sensor is joined by a four-year battery, screw or magnet mounting, and a wireless gateway from partner MultiTech that uses the LoRaWAN (long-range, wide-area network) communications protocol—all in one lightweight body.
The gateway receives measurements from XS770A, and passes them to a cloud or onsite server.
Sushi Sensor also provides IP 66-67 protection, as well as ATEX and IECEx intrinsic safety approvals. Other options include GA10 software that records and graphically displays measurements, and an NFC card for exchanging a cryptographic key for LoRaWAN communications.
“We did our research and standardized on LoRaWAN because its point-to-multipoint, and its 900-MHz range provides plant coverage up to one mile from one gateway. Plus, it maintains cybersecurity with 128-bit encryption. “This is not just a sensor widget,” says Kevin Zamzow, emerging solutions manager for North America at Yokogawa. “There are many commercial, off-the-shelf IIoT sensors, but few are industrially hardened for harsh environments, and even less have global approvals from FM in North America, and from ATEX and IECEx for intrinsic safety.”
Parameters for Sushi Sensor are easily set with a user-friendly software app on an android smartphone using near-field communications (NFC). It can then use LoRaWAN to collect data and continuously monitor devices in process applications without overlooking signs of abnormal behavior. This lets operators perform detailed diagnoses as needed, formulate appropriate responses, and focus their efforts and available time on these and other value-added tasks—even as the number of devices and operations increases.
“Process operations and maintenance users can use Sushi Sensor because of its combined and centralized functions,” explains Zamzow. “We also applied advanced machine learning (ML) algorithms to Sushi Sensor’s software that can run in the cloud or onsite, allow it to learn when the asset it’s monitoring is reaching an abnormal state based training during normal operation, and send health score to asset or work management programs to create work orders, or ERP systems to order parts.”
Zamzow reports Yokogawa has already released other IIoT Sushi Sensors for gauge pressure and temperature for thermocouples in Japan. These will be launched to other regions shortly. And, in the same way Sushi Sensor uses ML, Yokogawa has successful deployments using artificial intelligence (AI) to more precisely detect unusual conditions in stored data, and to simultaneously analyze sensor data, operations information and maintenance records. This will let Sushi Sensor detect signs of deterioration in equipment that can’t be detected with sensor data only. Indicators found will be fed back to operators, who can respond by adjusting operations balances and loads.
“Yokogawa has done wireless SCADA for a long time. The difference now is we’re putting its three main elements together,” adds Zamzow. “Other devices can try to predict performance, but with Yokogawa and solutions like Sushi Sensor, users get our longtime domain expertise, too. This means we can look at first principles, identify root causes, and correct conditions and processes that will lead to failures.”
For more information, visit www.yokogawa.com/us/ solutions/products-platforms/field-instruments/sushi-sensor
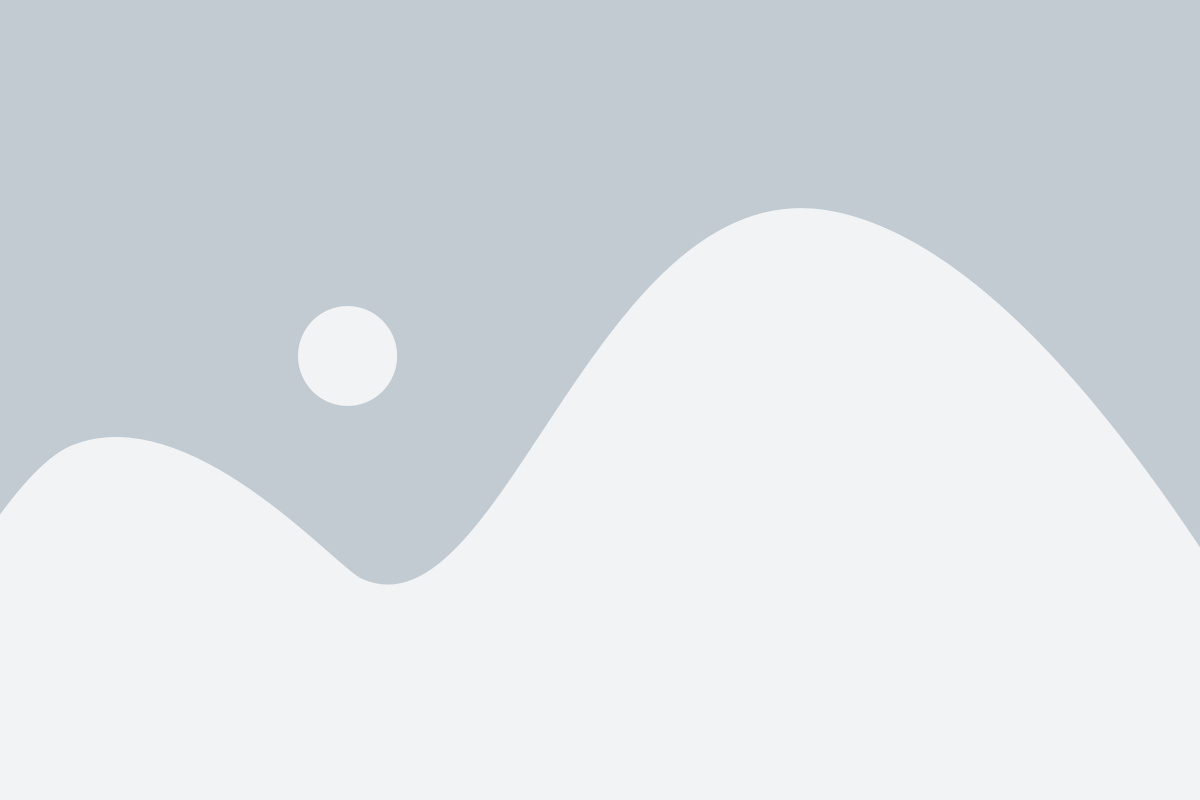