Volvo Group Implements a New Internet of Things (IoT) Network to Make Factories Smarter
Reducing operational costs and improving maintenance service is a huge concern for automobile manufacturers, and for the Volvo Group manufacturing facility in Lyon, France, this is no exception.
Volvo Group produces engines for different purposes, for instance for trucks , industrial power systems and boats, and the manufacturing process for these large, heavy engines relies on utilizing Autonomous Guided Vehicles (AGV).
To proactively monitor the health of the AGVs and prevent their shutdown, the IoT team at Volvo Group Digital & IT, supporting the factory in Lyon, envisioned a wireless system for predictive maintenance. The team initially looked at WIFI technology, but the WIFI 2.4GHz band was already being used for critical processes in the production line. Faced with this challenge, the IoT teamlooked toward LoRaWAN, a LPWAN protocol designed to connect battery-operated ‘things’ to the internet for powering the large fleet of AGVs. LoRaWAN is ideally suited to the manufacturing process as it provides long-range capability, good resistance to interferences, and a secured and flexible network architecture.
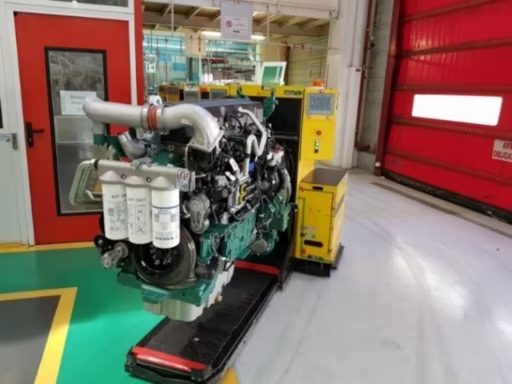
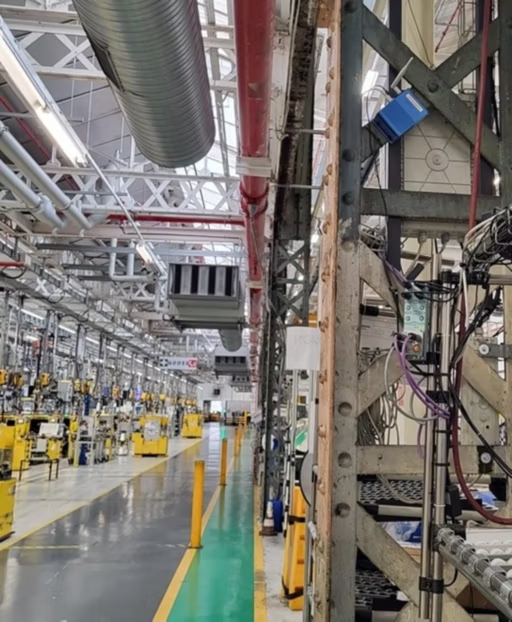
MultiTech gateway installed in the factory
To proactively monitor the health of the AGVs and prevent their shutdown, the IoT team at Volvo Group Digital & IT, supporting the factory in Lyon, envisioned a wireless system for predictive maintenance. The team initially looked at WIFI technology, but the WIFI 2.4GHz band was already being used for critical processes in the production line. Faced with this challenge, the IoT teamlooked toward LoRaWAN, a LPWAN protocol designed to connect battery-operated ‘things’ to the internet for powering the large fleet of AGVs. LoRaWAN is ideally suited to the manufacturing process as it provides long-range capability, good resistance to interferences, and a secured and flexible network architecture.
The team also installed their own LoRaWAN sensor on every AVG to receive periodic voltage data of the battery levels (<23V) or battery failures. With the new system, the maintenance team receives regular notifications, providing more time to move the AVGs to the charge point, without blocking the production line. They can also organize interventions in cases of battery failure.
"Implementing a radio infrastructure in our factory was a challenge, and we wanted to have a LoRaWAN network connected directly to our secure Ethernet network to avoid any cloud dependence. So, we have selected a Multitech industrial grade LoRa Gateway, with some edge computing capabilities and robust cybersecurity features to successfully qualify it through an complete IT audit”
Julien Bertolini | Principal Solution Architect IoTat Volvo Group Digital & IT